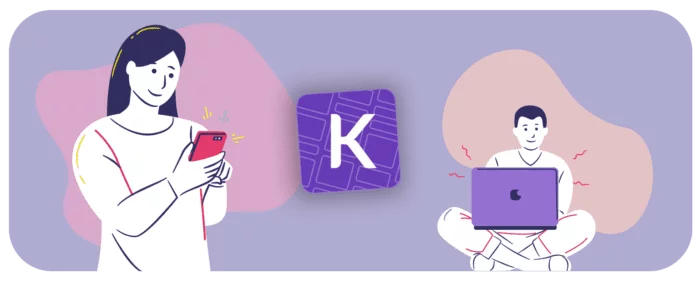
What is Kaizen?
Word “kaizen”, where “kai” = change “zen” = good, simply means “change for better”. In English kaizen typically means measures for implementing continuous improvement.
Kaizen is an approach to activity organization based on common sense, self-discipline, order, and economy. Kaizen method is a strong contributor and fundamental part of a lean production process model in lean manufacturing.
It is applicable to lean software development as well as to personal endeavors.
Want to try Kanbanchi?
Kaizen refers to any activities that continually improve all business functions or processes and involves every employee from the CEO to the assembly line workers. Labeling industrial or business improvement techniques with the word “kaizen” is a common practice in Japan. It also applies to processes, such as purchasing and logistics, that cross organizational boundaries into the supply chain.
With Kaizen management practices, the main priority is given to the manufacturing process, as the process of achieving results is not less than the final result. The reason for this focus is that imperfect processes could potentially not lead to achieving the goal. A corresponding task of kaizen is to become a part of the market by improving processes within the organization instead of pushing products into the market. One of the most important tasks in Kaizen involves improving the quality of work in an organization by achieving TQC (total quality control).
The kaizen method is now a base model for other quality improvement methods including suggestion systems, automation, small group activities, Kanban system, just-in-time, zero defects, total productive maintenance, total quality control, etc.
Kaizen History
The history of Kaizen begins after World War II when Toyota first implemented quality circles in its production process. American business and quality management teachers who visited the country back then partly influenced such implementation.
A quality circle is a group of workers performing the same or similar work, who meet regularly to identify, analyze and solve work-related problems. This revolutionary concept became very popular in Japan in the 1950s. Now it continues to exist in the form of Kaizen groups as well as similar worker participation schemes. The term Kaizen actually became famous around the world through the works of Masaaki Imai.
Masaaki Imai (born, 1930) is a Japanese organizational theorist and management consultant. His work on quality management, specifically on Kaizen is well-known. In 1985 he founded the Kaizen Institute Consulting Group (KICG) to help western companies introduce the concepts, systems, and tools of Kaizen. At present time, the Kaizen Institute team has applied the lean methodology and kaizen training courses to virtually all business sectors throughout the globe.
Masaaki Imai published two fundamental books on business process management. “Kaizen: Japanese spirit of improvement” (1985), which helped popularize the Kaizen concept in the West, and Gemba Kaizen: A Commonsense, Low-Cost Approach to Management (1997).
Kaizen Event
In modern usage, kaizen is designed to address a particular issue over the course of a week, which is referred to as a “kaizen blitz” or “kaizen event”. A kaizen event is a focused development project that can accomplish breakthrough improvements in a short amount of time, about 2-10 days in scope. Kaizen events must have a clear, concise objective along with immediately available resources and rapid results. This ensures the results are significant, clear, and quick to promote the generation of continued enthusiasm and satisfaction.
10 Principles of Kaizen
The Kaizen method follows ten specific principles, which are described below:
- Improve everything continuously.
- Abolish old, traditional concepts.
- Accept no excuses and make things happen.
- Say no to the status quo of implementing new methods and assuming how they will work.
- If something is wrong, correct it.
- Empower everyone to take part in problem-solving.
- Get information and opinions from multiple people.
- Before making decisions, ask “why”-questions five times to get to the root cause. (5 Why Method)
- Be economical. Save money through small improvements to spend the saved money on further improvements.
- Remember that improvement has no limits. Never stop trying to improve.
Kaizen method strives toward perfection by eliminating waste (Muda) in the workplace (Gemba). The goal of kaizen is production without wastes by improving standardized activities and processes. Industrial engineer Taiichi Ohno, the father of the Toyota Production System, noticed that there is an 80% loss in every process and the value of the process is less than 20%.
The Seven Wastes (Muda)
A portion of micro-processes functioning as part of the full process (from start to finish) does not make any transformation to the product that the consumer is willing to pay for. After analyzing manufacturing processes, Taiichi Ohno was able to identify which steps add value and which ones do not. As a result, he developed a better way for organizations to identify waste with his “Seven Wastes” model. These wastes include:
- Delay, waiting or time spent in a queue with no value being added. A large part of an individual product’s life is spent waiting to be worked on.
- Producing more than you need. Overproduction usually hides and/or generates all the others. It leads to excess inventory, which then requires the expenditure of resources on storage space and preservation. These activities do not benefit the customer.
- Over-processing or undertaking, non-value-added activity. Over-processing occurs when more work is performed on a piece than what is required by the customer.
- Transportation. Each time you move a product, it stands the risk of damage, loss, delay, etc. as well as to have a cost for no added value.
- Unnecessary movement or motion. The motion refers to the damage that the production process inflicts on the entity that creates the product. This may be either over time (wear and tear for equipment and repetitive strain injuries for workers) or during discrete events (accidents that damage equipment and/or injure workers).
- Inventory. Whether it is in the form of raw materials, work-in-progress, or finished goods, represents a capital outlay that has not yet produced an income, either by the producer or for the consumer.
- Production of Defects. Defects cause extra costs for reworking the part and can sometimes result in doubling the cost of one single product.
Gemba Kaizen
Genba (also romanized as Gemba) is a Japanese term that means “the real place”.
In lean manufacturing, the idea of Gemba is that the problems are visible and the best improvement ideas will come from going to the Gemba (the factory floor in manufacturing). The Gemba walk is an activity that takes lean management to the front lines to look for waste and opportunities to practice Gemba kaizen or practical shop-floor improvement.
The term Gemba, in international practice, became widely known after publications about the Toyota quality management system. In practice, if a problem occurs, the engineers must go to the source to understand the full impact of the problem, gathering data from all sources. Japanese decision-making principle differs from a traditional American management approach where you typically make decisions remotely.
The golden rule of Gemba management, called the 5-Gemba principles, is as follows:
- When a difficulty (abnormality) arises, consider going to Gemba first.
- Check with gembutsu (machines, tools, rejects, and customer complaints).
- Take temporary countermeasures on the spot.
- Find out the root cause. By repeating the question “why” several times, you can find out the root cause of the problem.
- Standardize for prevention of recurrence.
Kaizen in modern technologies
In today’s situation of having to manage multiple projects and to make decisions quicker, managers often try to apply the latest high-cost technologies to handle problems that can be solved with a commonsense, low-cost approach. The kaizen method involves the usage of simple tools, checklists, and techniques. It doesn’t require the investment of a great deal of money yet offers substantial benefits to any business. If you are a fan of technologies and understand that the kaizen approach is exactly what your organization needs to implement, you can adopt some online tools supporting the methodology. Kanbanchi is one of such tools.