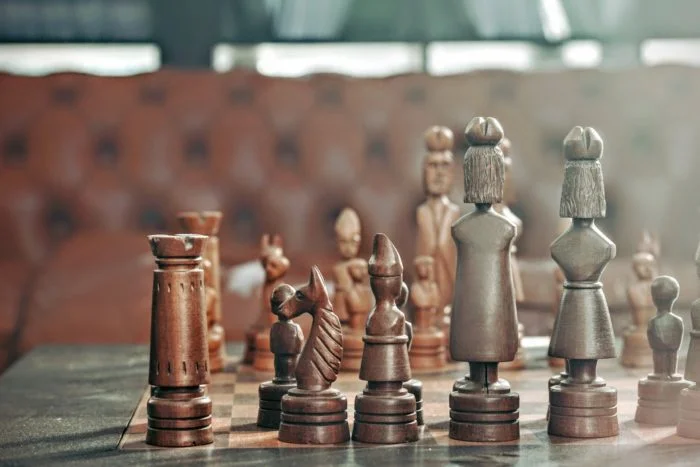
Что такое лин менеджмент?
Лин менеджмент — это популярный подход к управлению компанией, основанный на концепции постоянного совершенствования. Другими словами, это постоянные усилия по совершенствованию продуктов, услуг или процессов, которые требуют «постепенного» улучшения с течением времени для повышения эффективности и качества.
Основная цель бережливого менеджмента — уменьшить факторы, которые тратят впустую время, силы или деньги. Единственный способ справиться с этим — это проанализировать бизнес-процесс, а затем пересмотреть его и исключить каждый шаг, который не создает ценности для клиентов.
Принципы бережливого менеджмента
Принципы бережливого управления включают:
- Определение ценности с точки зрения конечного потребителя
- Выявление каждого шага бизнес-процесса и устранение тех шагов, которые не создают ценности
- Определение шагов по созданию ценности в тесной последовательности
- Повторение первых трех шагов на постоянной основе, пока не будут устранено все лишнее
Эти принципы лин менеджмента гарантируют, что производство и вывод на рынок останутся рентабельными.
Лин менеджмент или бережливый менеджмент — это систематический метод устранения потерь в производственном процессе. Например, потери могут быть вызваны неравномерностью рабочих нагрузок, перегрузкой или любой работой, которая не добавляет ценности. С точки зрения потребителя, «ценность» — это любой процесс или действие, за которые он готов заплатить. По сути, бережливое производство — это акцент на том, чтобы сделать очевидным то, что приносит пользу, уменьшив все остальное.
История лин менеджмента
Безусловно, сокращение расходов имеет долгую историю в обрабатывающей промышленности. Фактически, ключевые концепции лин менеджмента открывались и переоткрывались несколько раз на протяжении многих лет. Люди искали различные способы, чтобы избежать потерь. Но лин менеджмент как философия управления в основном пришло из производственной системы Toyota (TPS). Именно Джон Крафчик ввел термин «лин менеджмент» в статье «Триумф системы лин менеджмента» в 1988 году. Он написал эту статью на основе своей магистерской диссертации в школе менеджмента Sloan при Массачусетском технологическом институте. До учебы Крафчик работал инженером по качеству в Toyota-GM NUMMI.
Другой важной фигурой был Киичиро Тойода. Он был основателем Toyota Motor Corporation. Руководя работами по отливке двигателей, он обнаружил множество проблем в их производственном процессе. Он создал группы по совершенствованию «кайдзен», когда в 1936 году его процессы столкнулись с новыми проблемами. Toyota заявила, что главный метод бережливого менеджмента — это не инструменты, а сокращение трех типов расходов:
- муда («работа, не добавляющая ценности»)
- мури («перегрузка»)
- мура («неравномерность»)
Это помогает систематически выявлять проблемы и упрощает использование правильных инструментов там, где невозможно достичь идеала. Тайити Оно, японский промышленный инженер и бизнесмен, считается отцом производственной системы Toyota. Он предложил сосредоточиться на сокращении исходных семи расходов Toyota, чтобы улучшить конечный продукт.
Инструменты лин менеджмента
Выделяются многие элементы концепции лин менеджмента, и каждый из них представляет собой определенный метод:
- 5S
- Канбан (подтягивающие системы)
- Картирование потока создания ценности
- SMED
- Poka-yoke (защита от ошибок)
- Устранение временных задержек
- Комплексное обслуживание оборудования
- Смешанная модель
- Единое планирование
- Кластеризация в порядке приоритета
- Многопроцессная обработка
- Перепроектирование рабочих ячеек
- Контрольные диаграммы (для проверки “мура”)
Некоторые из этих методов, такие как кайдзен и канбан, превратились в независимые производственные концепции.
Кайдзен 5S
5S — идеальный способ справиться с расходами и повысить рентабельность. Буква «S» означает 5 слов: выстроить, отсортировать, стандартизировать, отшлифовать и поддерживать. Фактически, это перевод с оригинальных японских слов: seiton, seiri, seiketsu, seiso, и shitsuke. Эти слова описывают способы организации рабочего места для достижения максимальной эффективности. Например, идентификация и хранение бывших в употреблении предметов, обслуживание предметов и территории, а также поддержание нового порядка.
5S стал фундаментальной мерой бизнеса и ключевым фактором для Кайдзен. Пять шагов заключаются в следующем:
- Сортировка: отсортируйте и отделите то, что нужно и что не нужно в данной области
- Выстраивание: расположите необходимые предметы так, чтобы они были готовы к использованию. Четко определите место для каждого из предметов, чтобы каждый мог их найти и вернуть после выполнения задачи
- Шлифовка: Регулярно очищайте рабочее место и оборудование, чтобы поддерживать стандарты и вовремя выявлять дефекты
- Стандартизация: регулярно пересматривайте первые три из 5S и подтверждайте состояние Gemba, используя стандартные процедуры
- Поддержание: соблюдайте правила, чтобы поддерживать стандарты и постоянно совершенствоваться каждый день.
Канбан
Излишне говорить, что канбан — один из лучших способов сократить количество расходов. В 1952 году Тайити Оно изобрел в компании Toyota систему канбан, как систему для улучшения и поддержания высокого уровня производства.
Позже Канбан стал эффективным инструментом для поддержки производственной системы в целом. Кроме того, это отличный способ для улучшению процессов. Одним из основных преимуществ системы канбан является возможность установить верхний предел для запасов незавершенного производства. Это позволяет избежать перегрузки производственной системы. Канбан-концепция “to do” – “doing” – “done” стала краеугольным камнем многих онлайн-инструментов, используемых для управления проектами и контроля рабочих процессов. Канбанчи — один из таких инструментов, поддерживающих алгоритм Канбан. Если вам интересно, вы можете попробовать его сейчас и посмотреть, как это повысит вашу производительность.
Тайити Оно заявил, что канбан должен соответствовать строгим правилам использования, чтобы быть эффективным. У Toyota, например, есть шесть простых правил. Тщательный контроль за соблюдением этих правил — задача бесконечная. Это гарантирует, что система канбан выполняет то, что от нее требуется:
- На более поздних стадиях процесса собирается элементы, указанные Канбаном в процессе ранее
- На ранних стадиях товары производятся в количестве и в последовательности, обозначенной Канбаном
- Никакие предметы не производятся и не перевозятся без участия Канбана
- Всегда привязывайте к товарам Канбан
- Неисправные товары не отправляются на последующий этап процесса. Результат — 100% бездефектный товар
- Уменьшение количества канбанов увеличивает чувствительность процесса.
Картирование потока создания ценности
Картирование потока создания ценности — это метод лин менеджмента, который применим практически для любой цепочки создания ценности. Он используется для анализа текущего этапа и проектирования его дальнейших этапов для серии событий, которые проводят услугу или продукт от начала до конечного клиента. Этот метод также применим к:
- Логистика
- Цепочка поставок
- Сфера услуг
- Здравоохранение
- Разработка программного обеспечения
- Разработка продукта
- Административные или офисные процессы
В картировании потока создания ценности обычно используются стандартные символы для представления элементов и процессов. Лучший способ создать VSM — нарисовать карандашом на листе бумаги формата А3. Причина в этом то, что вам нужно будет часто вносить много исправлений и изменений.
Фактически, VSM — относительно недавнее дополнение к набору инструментов TPS. Даже в конце 1990-х эти методы были по большей части неизвестны за пределами Toyota. Позже Джон Шук и Майк Ротер стали соавторами книги «Учимся видеть», опубликованной Институтом лин менеджмента. Это сделало материалы широко доступными для использования за пределами Toyota.
Несомненно, картирование потока создания ценности — это гибкий инструмент, который позволяет нам разместить всю информацию в одном месте таким образом, что это невозможно с картированием процессов или другими инструментами. Прочтите эту статью, чтобы узнать о создании карты потока создания ценности.
Шесть Сигм
Определенно, сигма — это математический термин, который измеряет отклонение процесса от совершенства. Как и Кайдзен, «Шесть сигм» — это философия управления, направленная на постоянное совершенствование различных процессов. Билл Смит впервые представил этот термин в 1986 году в компании Motorola.
В отличие от Кайдзен, основной целью которого является повышение эффективности всех аспектов процессов, Six Sigma фокусируется на улучшении качества конечного продукта путем поиска и устранения причин дефектов. Six Sigma использует статистический анализ и стремится свести дефекты к нулю. Сигма-рейтинг описывает зрелость производственного процесса, указывая процент или выход бездефектных продуктов, которые он создает. Компаниям необходимо определить надлежащий уровень сигма для каждого из своих наиболее важных процессов и стремиться к его достижению.
Основным инструментом, используемым для реализации проектов шести сигм, является цикл улучшения DMAIC. DMAIC — это аббревиатура пяти этапов улучшения, которые он включает: определение, измерение, анализ, улучшение и контроль. Все шаги обязательны и всегда выполняются в указанном порядке.
DMAIC относится к управляемому данными циклу улучшения, используемому для улучшения, оптимизации и стабилизации бизнес-процессов и проектов. Пять шагов не являются уникальными для «Шести сигм». Таким образом, они могут служить основой для других процессов улучшения.
Концепция шести сигм утверждает:
- Достижение устойчивого повышения качества требует усилий от всей компании, особенно со стороны высшего руководства
- Производственные и бизнес-процессы обладают функциями, которые можно измерять, анализировать, контролировать и улучшать
- Постоянные усилия по достижению стабильных и предсказуемых результатов процесса (т.е. уменьшению вариативности процесса) имеют жизненно важное значение для успеха бизнеса
Помимо предыдущих функций, Six Sigma также устанавливает следующие инициативы по повышению качества:
- Четкое стремление принимать решения на основе поддающихся проверке данных и статистических методов, а не на предположениях
- Повышенный упор на сильное и увлеченное руководство и поддержку
- Четкая ориентация на достижение измеримой и количественной финансовой отдачи от любого проекта «Шесть сигм»
- В конце 1990-х годов более 60% компаний со статусом Fortune 500 начали применять «Шесть сигм». Таким образом, Motorola заявила об экономии около 17 миллиардов долларов с 2006 года как о прямом результате внедрения «Шести сигм».
В последние годы стало популярным использование идей шести сигм в сочетании с лин менеджментом. Таким образом, подход «лин менеджмент и шесть сигм» включает в себя «Шесть сигм» с акцентом на вариации и дизайн, а также лин менеджмент, который рассматривает вопросы потока и расходов как дополнительные дисциплины, направленные на продвижение бизнеса и функциональную эффективность.