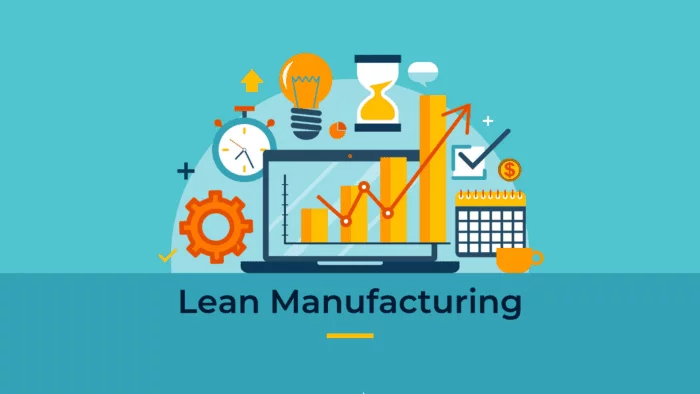
Metodologia de Gestão Lean
O que é o “lean manufacturing” ou produção enxuta?
Gestão lean, ou “lean manufacturing” em inglês, é uma filosofia popular em gestão de empresas. Assim como Kaizen, ela se baseia no conceito de melhoria contínua. Em outras palavras, é um esforço contínuo para aperfeiçoar produtos, serviços e processos. Ela requer melhorias incrementais ao longo do tempo, com o objetivo de aprimorar qualidade e eficiência na produção.
A principal forma de aprimoramento na gestão lean é a redução de desperdícios de tempo, dinheiro e esforços. Através da análise do processo produtivo, etapas que não geram benefícios ou adicionam valor ao produto são removidas.
5 Princípios da metodologia lean
Alguns princípios guiam a metodologia lean:
- Especificar o valor sob o ponto de vista do consumidor final.
- Identificar fluxo de valor, ou seja, cada etapa do processo de produção e eliminar os passos que não agregam valor.
- Criar fluxo contínuo de produção das etapas restantes (que agregam valor).
- Estabelecer “pull”, ou seja, centrar decisões de produção nos clientes e sua demanda.
- Buscar a perfeição através da repetição dos 4 primeiros princípios, gerando melhoria contínua.
Esses 5 princípios da produção lean garantem que a produção e lançamentos de produtos se mantenham efetivas em questão de custos.
A metodologia lean é uma filosofia de redução sistemática de desperdícios em um processo produtivo.
Por exemplo, desperdícios podem ser originados pela má distribuição de mão de obra, sobrecarregamento, ou qualquer atividade que não gere valor. Do ponto de vista do consumidor, existe geração de valor quando o cliente se dispoe a pagar mais pelo produto ou serviço.
Basicamente, o sistema de gestão lean se resume em identificar as etapas do processo produtivo que geram valor. Ao limitar ou extinguir os que não geram, há um aumento de produtividade.
História do Lean – Toyota production system
A redução de despedícios tem uma história considerável na produção industrial. Na verdade, os princípios e conceitos da gestão lean foram descobertos e redescobertos diversas vezes durante a história. Entratanto, produção enxuta como filosofia de gestão tem origem na indústria automobilística, mais especificamente no Sistema Toyota de Produção.
John Krafcik foi quem introduziu o termo “lean” no seu artigo “Triunfo do Sistema de produção Lean”, em 1988. O artigo foi escrito como base da sua tese de mestrado no MIT. Antes de ser mestrando, ele havia trabalhado como engenheiro de qualidade na NUMMI, joint venture da Toyota e da General Motors.
Outra importante figura na história da metodologia lean de gestão foi Kiichiro Toyoda, fundador da montadora japonesa Toyota. Enquanto diretor do serviço de fundição de motores, ele encontrou diversos problemas no seu processo de produção. Ele então criou times de melhoria “Kaizen”, ao encontrar novos problemas na produção em 1936.
A Toyota reconhece 3 principais tipos de desperdícios como sendo os mais importantes a serem superados:
- muda (atividades que não agregam valor)
- muri (sobrecarga)
- mura (desequilíbrio)
As ferramentas da gestão lean
Diversos elementos dentro do conceito de produção enxuta se destacam, cada um deles com seus métodos particulares:
- 5S
- Kanban (pull systems)
- Value Stream Mapping
- SMED
- Poka-yoke (prova de erros)
- Elimination of Time Batching
- Total Productive Maintenance
- Mixed Model Processing
- Single Point Scheduling
- Rank Order Clustering
- Multi-process Handling
- Redesigning Working Cells
- Control Charts (para checar o mura)
Alguns desses métodos, como o Kaizen e o Kanban cresceram e se tornaram conceitos de produção indenpendentes.
Kaizen 5S
5S é uma forma perfeita de lidar com desperdícios e aumentar produtividade. A letra “S” representa 5 palavras: Seiri (utilização), Seiton (organização), Seiso (limpeza), Seiketsu (padronização), e Shitsuke (disciplina). Essas palavras descrevem a forma para alcançar a maior eficiência no ambiente de trabalho.
- Seiri (utilização): separe o que é necessário do que não é na área de trabalho.
- Seiton (organização): Organize os items que sei necessários para que estejam prontos para serem facilmente utilizados. Designe um lugar para colocar todos os itens para que todos possam encontrá-los e para onde devem devolvê-los ao completarem a tarefa.
- Seiso (limpeza): Limpe o espaço de trabalho equipamentos regularmente de forma a manter um padrão e identificar defeitos o mais breve possível.
- Seiketsu (padronização): Revisite os 3 primeiros itens de forma regular e confirme as condições do Gemba usando processos padrões.
- Shitsuke (disciplina): Mantenha as regras em ordem para garantir o padrão e continuamente melhorá-los diariamente.
Kanban
A gestão visual do Kanban é hoje um dos melhores métodos de melhoria contínua para redução de desperdícios. A metodologia Kanban foi inventada em 1952 por Taiichi Ohno para melhorar e manter o nível de produtividade nas fábricas da Toyota.
Mais tarde, Kanban se tornou um sistema de produção completo, se tornando um excelente sistema de melhoria contínua. Uma das maiores vantagens do Kanban é a capacidade de evitar o multi-tasking. Com a possibilidade de limitar o work-in-progress (trabalho em andamento), o Kanban permite evitar a sobrecarga do sistema de produção.
O Kanban usa o conceito de colunas para gerenciar as etapas do processo de produção. Geralmente nominadas de “a fazer”, “fazendo” e “feito”, as colunas são compostas de cartões, que representam tarefas. Conforme as tarefas avançam, elas são movidas de uma coluna para a outra.
Esse sistema virou a base para muitas ferramentas de gerenciamento de projetos. O Kanbanchi é uma dessas ferramentas.
Taiichi Ohno também declarou que, para ser eficaz, o Kanban deve seguir rígidas regras de uso. A Toyota, por exemplo, tem seis regras simples. O monitoramento rigorosa dessas regras é uma tarefa constante que garante que o Kanban mostre os resultados esperados:
- Um processo capta o mesmo número de itens indicados no quadro Kanban na etapa anterior.
- O processo anterior produz o número de itens na quantidade e ordem indicadas no Kanban.
- Nenhum item é feito ou transportado sem estar indicado no Kanban.
- Sempre crie anexe o Kanban a cada mercadoria.
- Produtos defeituosos não são enviados para o processo subseqüente. O resultado é uma mercadoria 100% livre de defeitos.
- A diminuição do número de Kanbans aumenta a sensibilidade.
Value Stream Mapping (mapeamento do fluxo de valor)
O mapeamento do fluxo de valor é um método de gerenciamento enxuto que é aplicável a quase toda cadeia de valor. Ele é utilizado para analisar o estágio atual e projetar seus estágios posteriores para a série de eventos que levam um serviço ou produto desde o início até o cliente. Este método também é aplicável a:
- Logística
- Cadeia de suprimento
- Indústria de serviços
- Saúde
- Desenvolvimento de software
- Desenvolvimento de produtos
- Processos administrativos
Mapeamento do fluxo de valor geralmente emprega o uso de símbolos padrões para representar itens e processos. A melhor forma de criar um mapa de fluxo de valor é desenhando numa folha A3 com um lápis. A razão para isso são as frequentes correções e mudanças que terão de ser feitas.
O mapeamento do fluxo de valor é relativamente recente na caixa de ferramenta do Sistema de Produção Toyota. Até o fim da década de 1990, essas técnicas eram pouco conhecidas fora da montadora. O sistema se difundiu externamente quando John Shook e Mike Rother publicaram o livro “Learning to see“, em conjunto com o Lean Enterprise Institute.
Value stream mapping é uma ferramenta flexível que permite colocar todas informações em um só lugar, de um forma que não é possível com outras ferramentas. Nesse artigo (em inglês) você pode encontrar mais informações sobre como criar um mapa de fluxo de valor.
Six Sigma
Six Sigma é um termo matemático para a medida de desvio da perfeição. Assim como Kaizen, Six Sigma éuma filosofia de gestão lean focada em criar e trazer melhoria contínua a diversos processos. Ela foi originalmente introduzida na Motorola em 1986 por Bill Smith.
Diferentemente do Kaizen, cujo principal objetivo é o aumento de produtividade em todos aspectos dos processos, o Six Sigma foca em melhorar a qualidade do produto encontrando e eliminando as causas de defeitos. Usando análises estatísticas, o método busca completamente eliminar defeitos. A classificação Sigma representa a maturidade do processo de produção indicando o percentual produzido de produtos sem nenhum defeito. Empresas precisam determinar um nível Sigma apropriado para cada um de seus processos, e então buscar alcançá-lo.
A principal ferramenta utilizada no Six Sigma é cíclo de melhoria DMAIC. Em inglês, a sigla representa Define (definir), Measure (medir), Improve (melhorar), e Control (controlar). Todas etapas são essenciais no processo e são executadas na ordem listada.
DMAIC é um cíclo de melhoria impuslionado por dados para melhorar, otimizar e estabilizar processos e designs. Esses cinco passos não são exclusivos do Six Sigma, de forma que podem servir de base para outras aplicaçoes de melhoria.
A metodologia Six Sigma estabelece alguns preceitos:
- Atingir aumento de qualidade sustentável requer esforços de toda a empresa, especialmente do alto escalão.
- Processos produtivos e de negócios tem características que podem ser medidas, analisadas, controladas e aprimoradas.
- Esforços contínuos para atingir resultados de processos que são estáveis e previsíveis (por exemplo, reduzir variações) são vitais para o sucesso de negócios.
- Um comprometimento claro em tomar decisões com base em dados verificáveis e método estatísticos em vez de suposições e adivinhações.
- Uma maior ênfase na liderança e no apoio à gestão forte e entusiasmada.
- Um foco claro na obtenção de retornos financeiros mensuráveis e quantificáveis de qualquer projeto Six Sigma.
No final dos anos 90, mais de 60% das empresas com o status de Fortune 500 começaram a aplicar o Six Sigma. Como resultado direto da sua implementação, a Motorola declarou uma economia de cerca de 17 bilhões de dólares desde 2006.
Nos últimos anos, tornou-se popular a utilização de ideias Six Sigma combinadas com a produção lean. Assim, a abordagem Lean Six Sigma inclui o Six Sigma, com seu foco na variação e design, e o pensamento lean, que aborda questões de fluxo de processo e desperdício como disciplinas extras destinadas a promover os negócios e a eficiência funcional.